News from EJOT UK
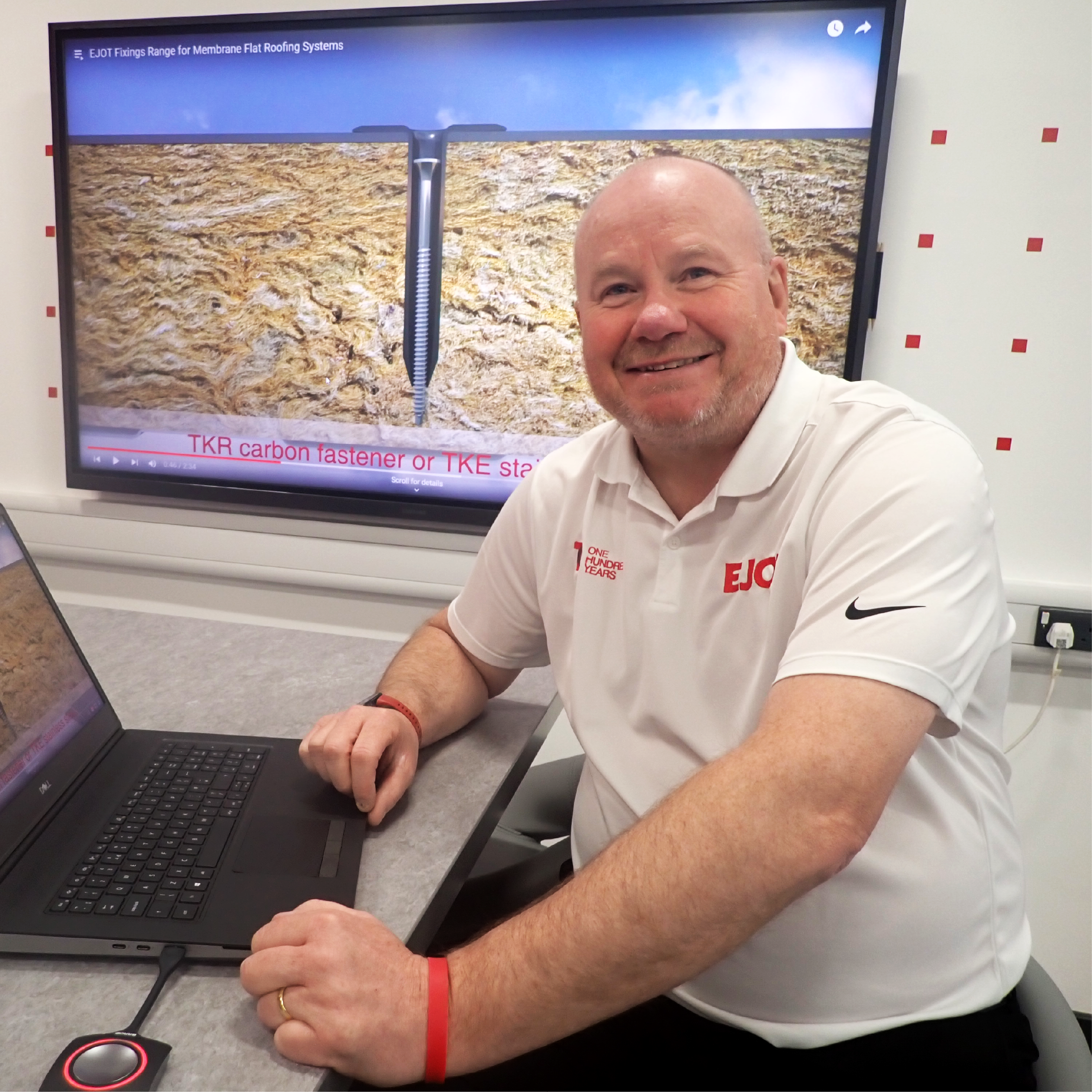
Is growth within the UK flat roofing sector on the horizon for EJOT UK?
Kevin Rackley would say so! After 21 years in a technical sales role, for the majority of that time as the company’s regional sales engineer for the South Wes, Kevin will step up into the new role of Business Development Manager for Flat Roofing Systems.