Achieving radical EV seating designs with superior performance
Steve Wynn, UK Sales Manager at EJOT explains why advanced fasteners are enabling the creation of exciting new seating designs in electric vehicles (EVs) without compromising other key design objectives for the vehicle.
Automotive seating has advanced significantly in recent years as technology and innovative materials have expanded the role it plays in a vehicle’s comfort level, its safety, overall weight, durability and interior styling.
As a result, drivers have come to expect seating with high levels of functionality coupled with modern and often radical styling, whether that is one of the latest generation of fuel-efficient internal combustion engine (ICE) vehicles or an electric vehicle (EV). Seats with heating and ventilation are no longer solely the domain of premium quality, luxury vehicles. Nor is the expectation for plenty of adjustability to support a safe, healthy and comfortable driving position.
Reflecting their advancement technologically, EV buyers have come to expect the vehicle to be packed with interior features, and the seat is no exception. But for designers to meet multiple criteria in the seating’s construction without adding significant weight to the EV can be a challenge.
In the pursuit of weight reduction, more innovative materials are being selected for the seat’s construction, including EPP (expanded polystyrene) and lighter alloys. This is by no means a revolutionary step because weight minimisation has been an increasingly important factor in recent decades to improve the fuel efficiency of ICE powered vehicles. It is, however, crucially important in EV design given the need to maximise the vehicle’s battery range.
Passive safety is a key objective too. As automotive seating must be designed with a high degree of structural strength to protect drivers and passengers in the event of a collision or impact, any design or material considerations must not compromise this fundamental factor.
The role of fasteners in EV seating
Key to delivering robust, feature-packed seating for EVs are innovative fastening solutions from EJOT. Our range enables designers to overcome many different joining challenges throughout the vehicle for proven performance, as has been demonstrated for decades with the world’s leading manufacturers of ICE, hybrid and electric powered vehicles.
Every seat will require a mix of different fastener types to suit the various materials used in its construction, electronics components, and mechanical elements. The key to optimising the seat’s design and manufacture is to understand which types of screw or other joining elements will enable the finished assembly to meet the necessary performance goals – both for the seating and vehicle overall.
Whether the assembly requires small diameter screws for use with climate control elements within the seat, larger screws for securing the seating rail to the frame or fixings for lumbar support or seat adjustment mechanisms, the EJOT range offers dependable solution throughout.
Most importantly, the EJOT automotive fastening solutions range provides products to achieve multi-material joints within the seat’s construction. Achieving the required performance may be possible with one screw type, rather than a combination of components, such as when forming a thread in plastics using the EJOT Delta PT.
What makes the Delta PT screw ideal for EV seating is that it is a fastening element designed for reliable and easy direct assembly into thermoplastics – even highly loaded thermoplastic materials. Its design will, therefore, accommodate the very high loads which components used in automotive applications often have to withstand.
Where lightweight alloys are used within the seat, there may also be the requirement for a screw capable of forming a thread. Here, the EJOT ALtracs Plus can be used to achieve a secure joint. It is a thread-forming screw specifically designed for light metal with an optimised thread geometry that facilitates the use of smaller and shorter screws. This is achieved with consistently high strength values and clamp loads for long term stability, even under high dynamic and thermal stress.
EJOT’s versatile range of fastening solutions for EPP foam provides automotive seating designers with options for utilising this lightweight material with confidence. Called EJOT EPPsys, this is a family of plastic fastening elements which offers an exceptional strength to weight ratio, durability, application versatility, optimisation for automated assembly, and recyclability.
The range includes the EPPsys RSD boss, a fastening element that is securely installed into foam via a friction welding process, and the EPPsys DR fastener for thin-walled components where a snap-fit connection is required. Both illustrate the potential for the application of EPP foam for seating designers to achieve creative results without weight gain.
Another innovative fastening solution that is facilitating the increased use of light weight foam and composite materials with a good strength-to-weight ratio is the EJOT TSSD. This thermal adhesive bonding boss is designed to provide a secure boss for the EJOT Delta PT screw or a direct fastening element, as well as EJOFORM bespoke cold formed fastening elements.
Whichever EJOT screws or fastening systems are specified for EV seating, designers have the assurance of a brand that is renowned for quality and excellent performance. As part of our extensive design support, we also offer product-specific calculation software which is available to automotive designers. These include Delta CALC – for the EJOT Delta PT screw for thermoplastics – and ALtra CALC for ALtracs Plus, a screw for thin-walled materials.
This technical support, coupled with amongst the most advanced fasteners available to the automotive industry, means we can help designers make time and cost savings at the development stage and throughout production.
What to know more? Read about the fasteners featured in this article:
- Fastening into honeycomb & foam structures
- ALtracs Plus - The self-tapping screw for light metal
- ALtra CALC & DELTA CALC - Prognosis software that can accelerate R&D programmes
- Delta PT – The high load capacity screw for direct fastening into plastics
- EJOFORM - Flexibility with multi-stage forming technology
- TSSD - Secure fastening solutions for honeycomb and foam composites
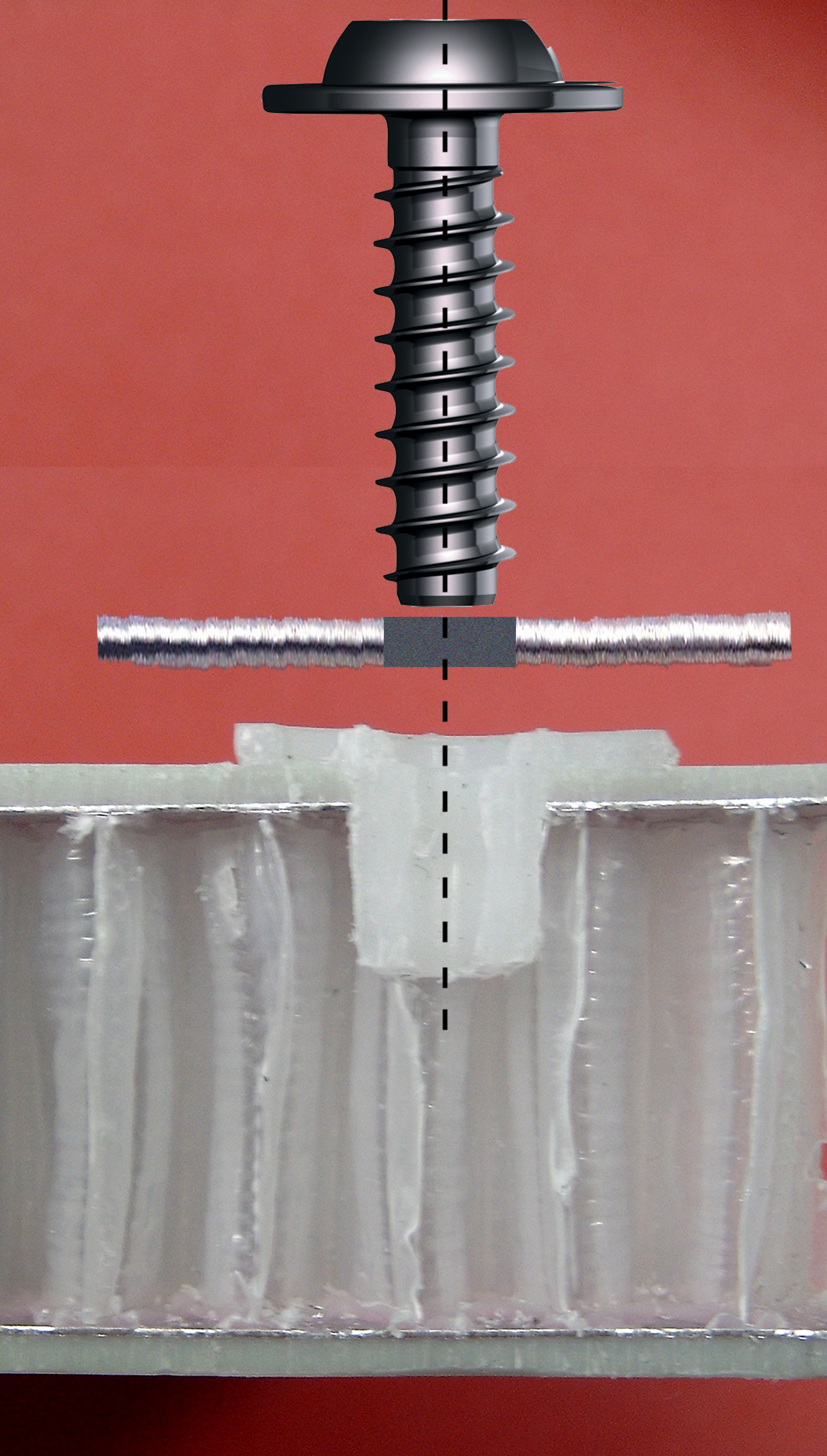
EJOT EPPsys plastic elements provide a solution for fastening into lightweight materials routinely used in EV seating construction – shown here in combination with the EJOT Delta PT screw.